정밀성∙내구성∙지속성이 극대화된
2차전지 믹싱 프로세스
제일엠앤에스만의 엔지니어링 기술력을 바탕으로 원료 이송량을 정확하게 제어하고 확인하는 계측제어 기술과 원료의 성분이 배관과 만나 영향 받지 않도록 철저한 재질선정 기술을 제공하며 원료 변경에 능동적으로 대응 가능하도록 전체 프로세스를 설계합니다.
공정 개요


2차전지 믹싱 공정은 원료 투입부터 코팅공정의 슬러리 공급까지 전 과정이 자동화 라인으로 구성되어 있어, 각 공정 단계별 품질 확인과 변경점 관리가 매우 중요한 공정입니다.
기술 강점
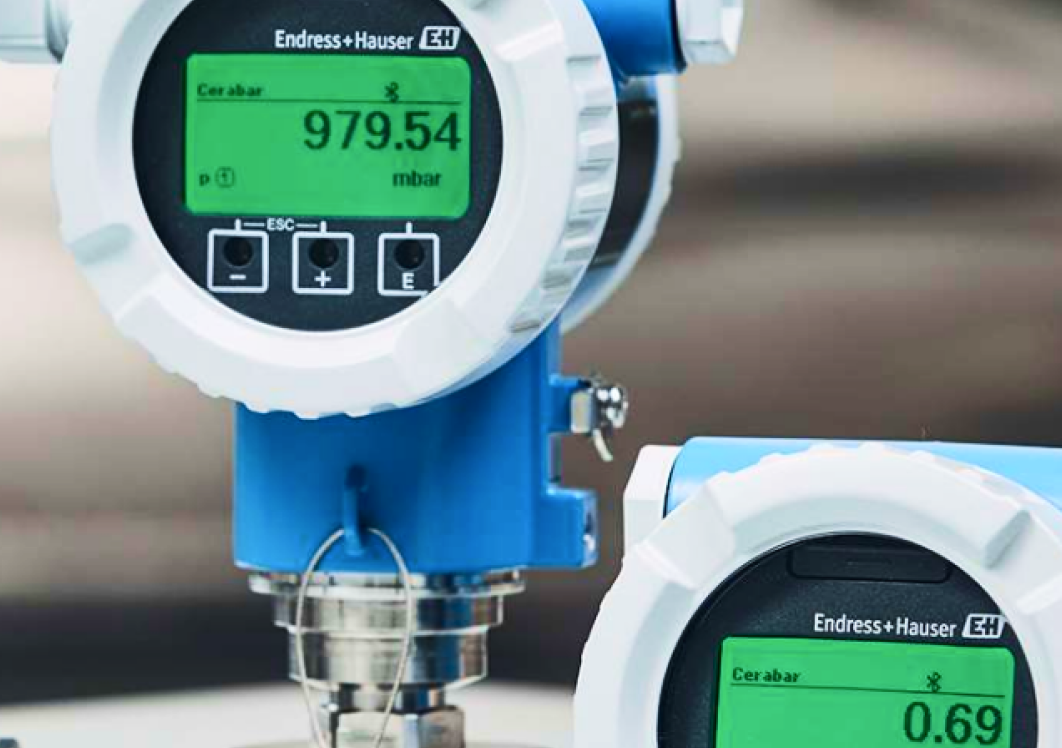
실시간 품질측정 시스템 적용
일반적으로 연속된 폐루프 배관라인으로 연결된 전극 슬러리 제조공정은 각 단계별로 슬러리 품질을 측정하여 불량제품이 이후 공정으로 유입되지 않도록 작업자가 수동으로 품질측정을 실시합니다. 이러한 긴 시간을 투입하여 점검하던 작업을 개선하여 제일엠앤에스는 배관라인의 실시간 연속 품질 측정 시스템을 적용하여 생산효율을 크게 증진시켰습니다.
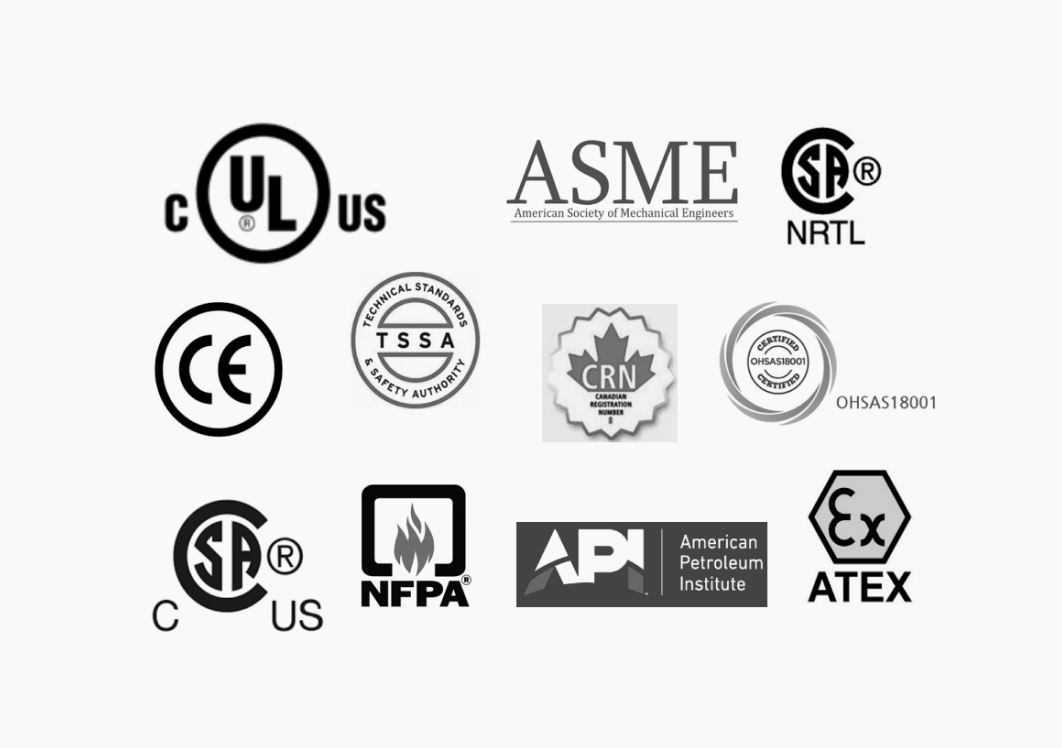
분진발생 및 폭발방지 기술 적용
전극을 제조하는 원료는 파우더 형태의 분체 원료와 액체 원료로 구분되는데, 특히 분체 원료의 경우 이송, 저장계량, 공급 과정에서 미립분체의 마찰에 의한 분진폭발이 발생할 수 있는데 이에 대한 방지 방안과 더 나아가 미립분체의 누출에 의한 작업자 위생안전 확보가 매우 중요하며, 이를 방지하기 위한 각 국가의 규정을 준수하여 설계/제작 및 설치공사를 완수하고 있습니다.
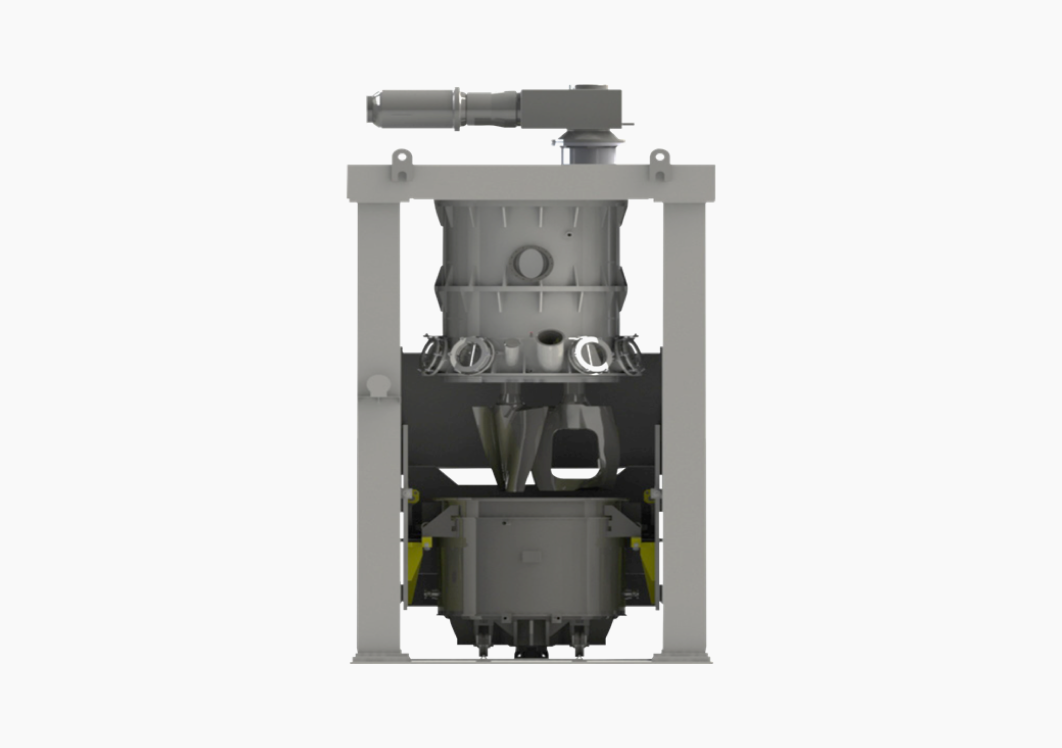
최적 효율의 믹싱 블레이드와 단위 생산성 향상기술 구현
2차전지의 성능과 생산성이 빠르게 향상되고 있기 때문에, 고형분 함량이 지속적으로 올라가고 있고, 메인 믹서의 배치당 생산용량이 커져 믹싱설비의 생산성 확보와 구동부의 내구성 확보가 중요한 인자가 되었습니다. 제일엠앤에스의 메인 믹서는 방산부문의 초고점도 슬러리 믹싱기술을 확보하여 이를 기반으로 한 고형분 함량 증가에 선제적으로 대응이 가능하고, 대용량 생산 메인 믹서를 양산라인에 적용하였습니다.
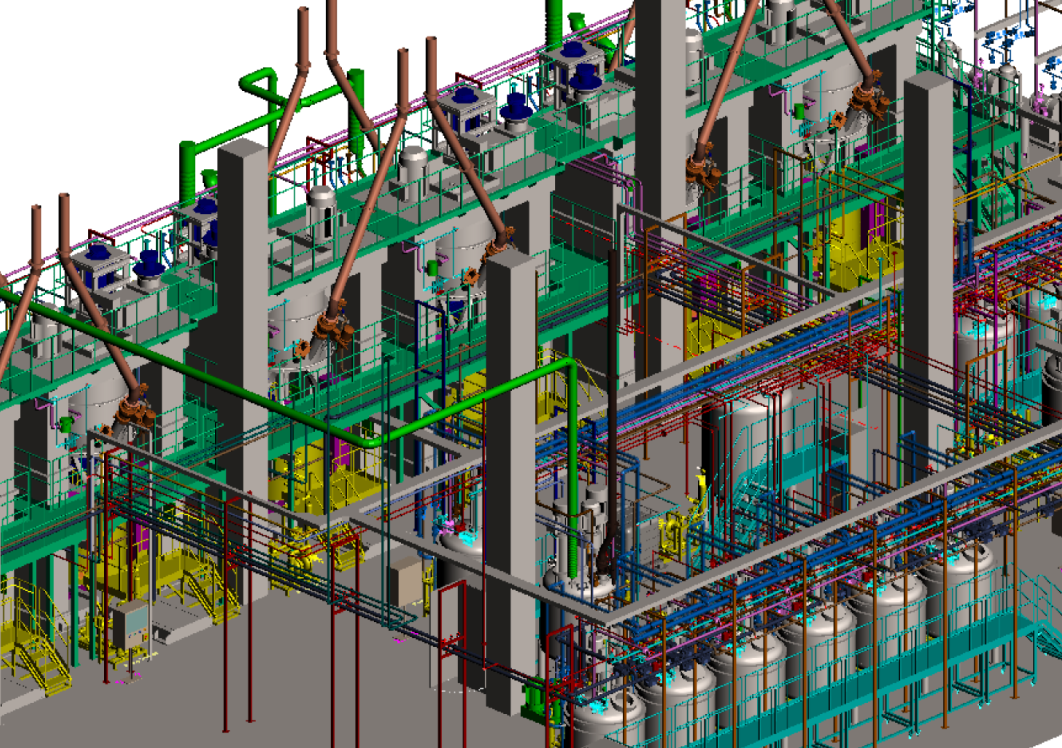
3D Modeling을 활용한
설치 전 간섭부위 확인
일련의 연속공정으로 이루어진 2차 전지 믹싱 프로세스는 각 장비와 연계된 복잡한 배관과 덕트 등으로 구성되어 있어, 설치공사 시 간섭에 의한 공사기간 지연을 방지하기 위해 전 공정에 대한 배관, 덕트 등을 3D 설계하여 간섭관계를 사전에 제거합니다.
공정 상세
- STEP 1원료 이송 및 저장
활물질, 바인더, 도전재, 용매 등 각각의 양극재 및 음극재 원료를 입고하여 다양한 이송방법을 통해 저장 호퍼에 저장하는 단계입니다.
- STEP 2계량
음극 및 양극 슬러리를 구성하는 각기 다른 원료를 요구하는 레시피 양 만큼 자동으로 계량하여 믹서로 공급하는 단계입니다.
- STEP 3선분산
바인더 또는 도전재 등 믹싱시간이 많이 소요되는 공정을 선행으로 믹싱하여 저장하며, 메인 믹서로 요구하는 시간에 맞춰 공급하는 단계입니다.
- STEP 4믹싱
전극 제조를 위한 메인 믹싱공정으로, 선분산 바인더와 활물질, 도전재 및 용매를 믹싱하여 슬러리를 제조하는 단계입니다.
- STEP 5슬러리 저장
메인 믹서에서 제조된 슬러리를 저장 또는 버퍼링하는 단계입니다.
- STEP 6코터 공급
저장된 슬러리를 코팅공정에서 요구하는 양에 맞춰 코터로 공급하는 공급탱크로 슬러리를 코터로 공급하는 단계입니다.